The Scion Innovation Hub in New Zealand proves that timber buildings have to be built in exactly the same way as steel and concrete buildings. The world’s largest diagrid structure made of laminated veneer lumber reduces the amount of wood required by 75 per cent and even withstands earthquakes.
The three spires on the front of the new building are visible from afar. They represent the three local Maori tribes, whose famous ancestor Tuteata gave the building its name: Te Whare Nui o Tuteata, which means “the great house of Tuteata”. These spires mark the entrance to one of the most innovative timber buildings of our time, located in the city of Rotorua on the North Island of New Zealand. The Scion Innovation Hub has a resource-saving timber structure that utilises the branches of a tree for structural support.
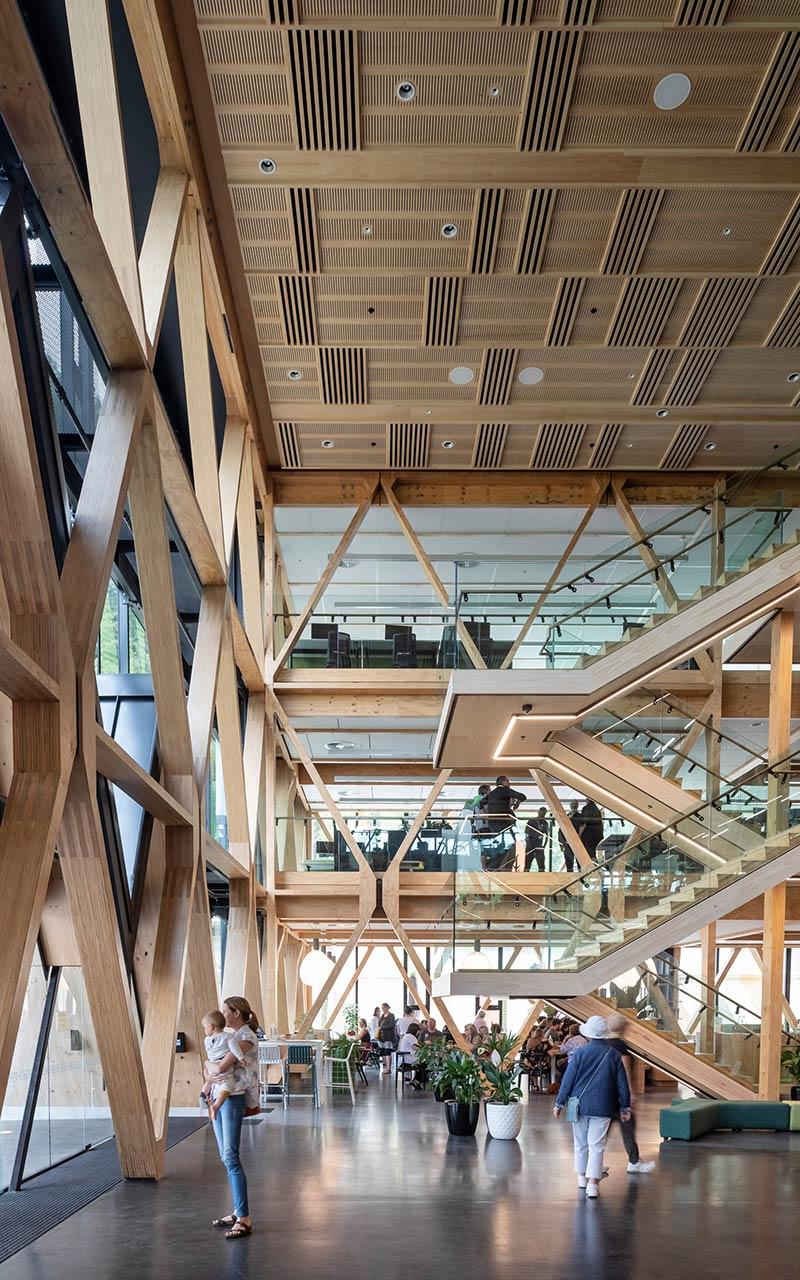
Very rarely is a branch perpendicular to the trunk. It usually runs diagonally, which reduces the load, and this ratio between horizontal and vertical load transfer is the key to strength.
Richard Naish, Architect
Very rarely is a branch perpendicular to the trunk. It usually runs diagonally, which reduces the load, and this relationship between horizontal and vertical load transfer is the key to strength,” explains Richard Naish, architect and founder of RTA Studio. The architectural firm, which has offices in three locations in New Zealand, was responsible for the design of the building together with Irving Smith Architects.
A wooden building as an excursion destination
The building, which is transparent throughout, impressively demonstrates what is possible today with the new wood-based materials. It serves as an illustrative case study for the Scion Timber Research Institute, which is housed here, and as a new attraction for the city. And indeed, the multi-award-winning building has become a real magnet for visitors since its opening in 2021. Day trippers come for lunch in the public café after a walk in the neighbouring Whakarewarewa Forest, while industry and government representatives gather inspiration and know-how for construction practice.
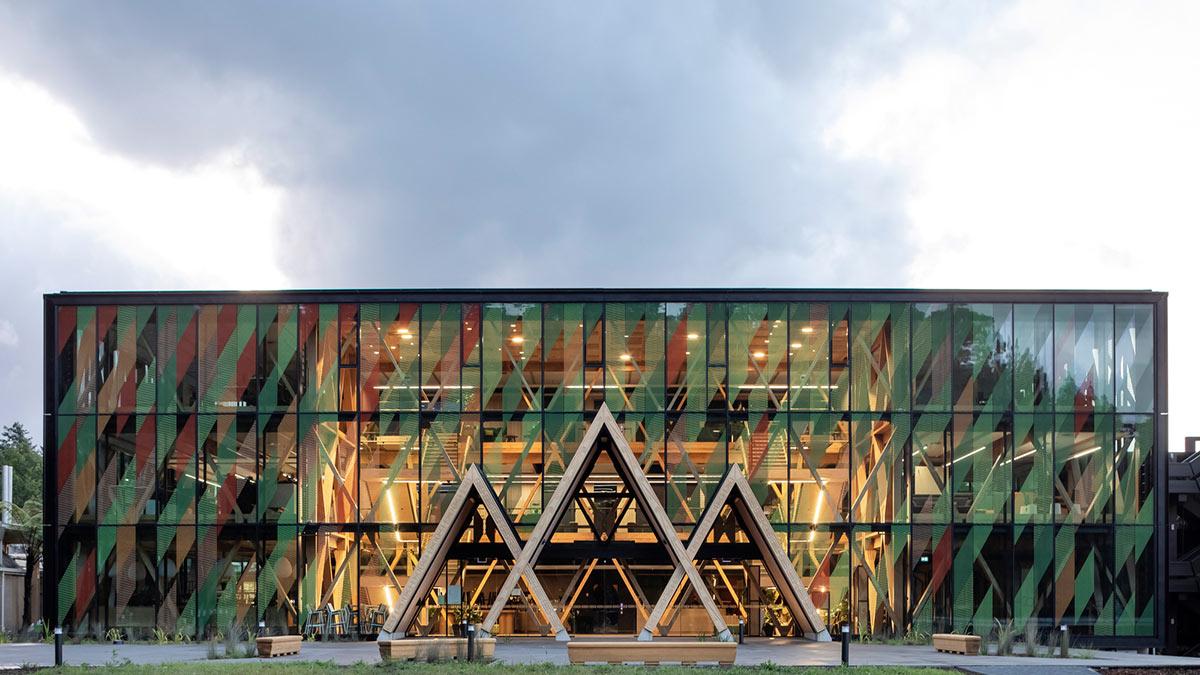
The unusual design is immediately apparent on entering the building. The striking diagrid structure, which extends across all three floors, is visible in the high airspace of the lobby. Visitors to the centre do not need much explanation as to what is supported by which components.
The diagrid elements transfer the load to the retaining rings, which give way in the event of an earthquake and can be replaced.
Richard Naish, Architect
The construction visible throughout the building is virtually self-explanatory. Only the oval steel bands, which are positioned laterally between the individual timber components, would have to be explained by the timber construction engineers responsible.
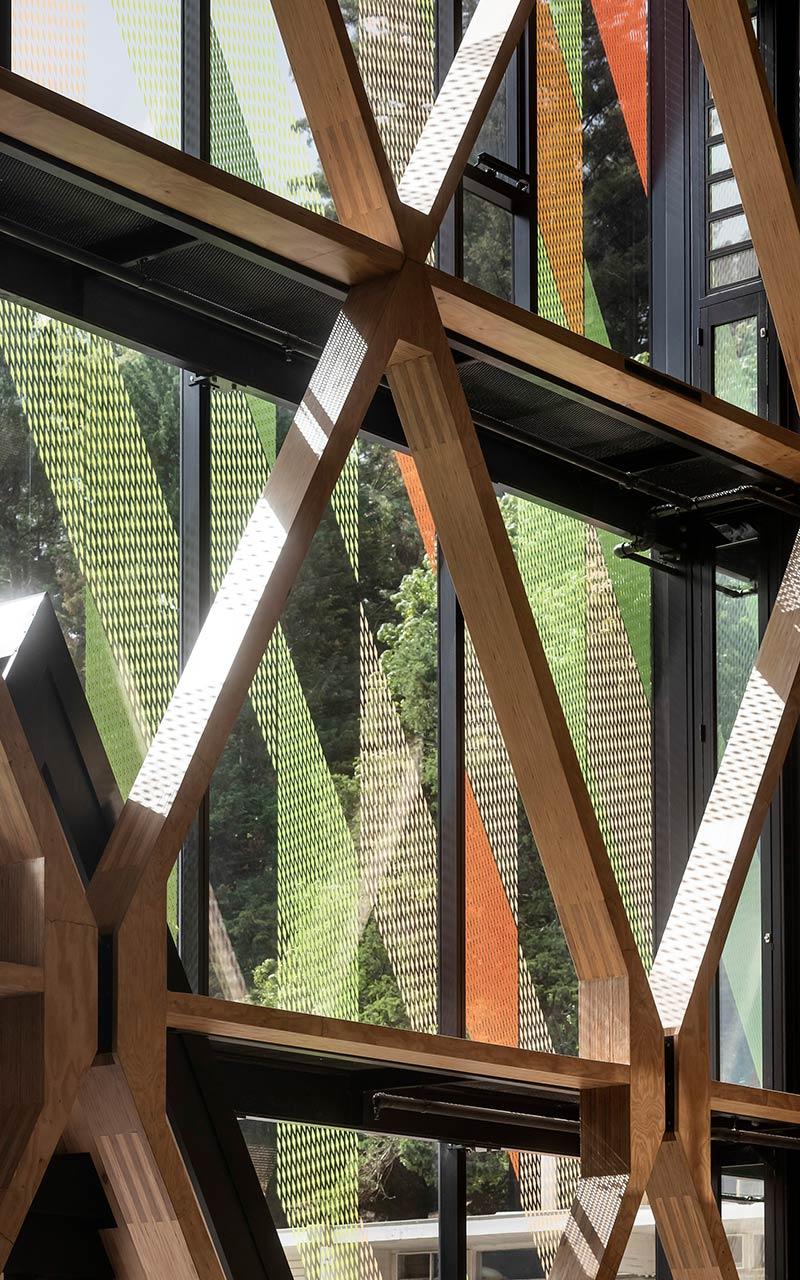
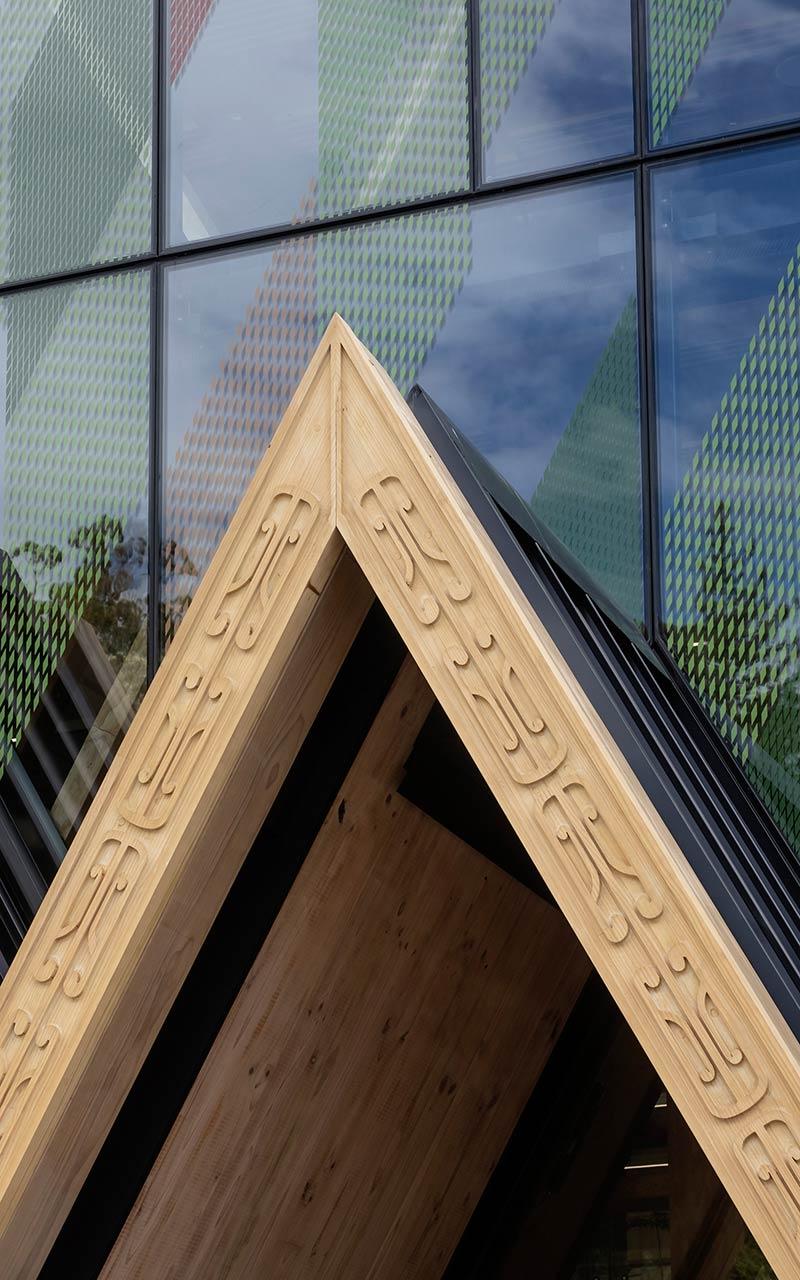
Architect Naish solves the puzzle in the accompanying project film: “The Diagrid elements transfer the load to the retaining rings, which give way in the event of an earthquake and can be replaced.”
World’s largest diagrid structure
The load-bearing structure consists of 4,248 components, which were prefabricated into 88 triangular frames at the factory. Instead of metal connections, the architects opted for wooden dovetail joints, especially as the brief was to create a wooden building that was as innovative as possible. They used high-performance laminated veneer lumber (LVL) in the construction, while the ceilings on the upper floors consist of cross-laminated timber elements.
According to RTA Studio, the construction system is the world’s first building of this size with a diagrid structure made of wood. This type of diagonal lattice structure has already proven itself in steel construction, with “The Gherkin”, Norman Foster’s parabolic skyscraper in London, as a prominent example. The diagrid structure should also be able to help timber construction reach new heights, as the River Beech Tower concept study by Perkins+Will shows. According to the study, this construction method can enable timber high-rise buildings to reach a height of 280 metres.
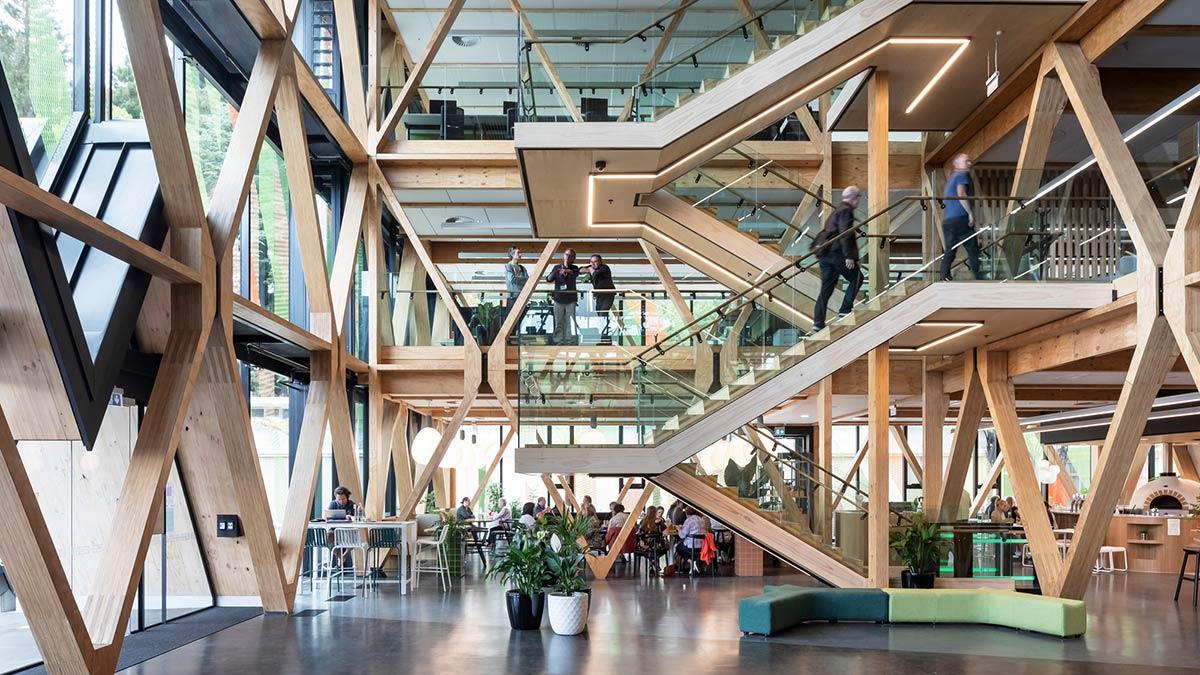
Co2-neutral construction
A major advantage of the diagrid structure is the slim supporting structure, which reduces the amount of material required. In the case of the Scion Innovation Hub, there is also the particularly resilient laminated veneer lumber, which saves even more material. “We have developed a construction system that reduces the size of the wooden components by 75 per cent,” says Naish in the video presentation of the project.
We have developed a construction system that reduces the size of the timber components by 75 per cent.
Richard Naish, Architekt
The wood used also stores around 500 tonnes of CO2. Together with the other materials, this results in a CO2-neutral construction method, as a test by the Etool system has shown.
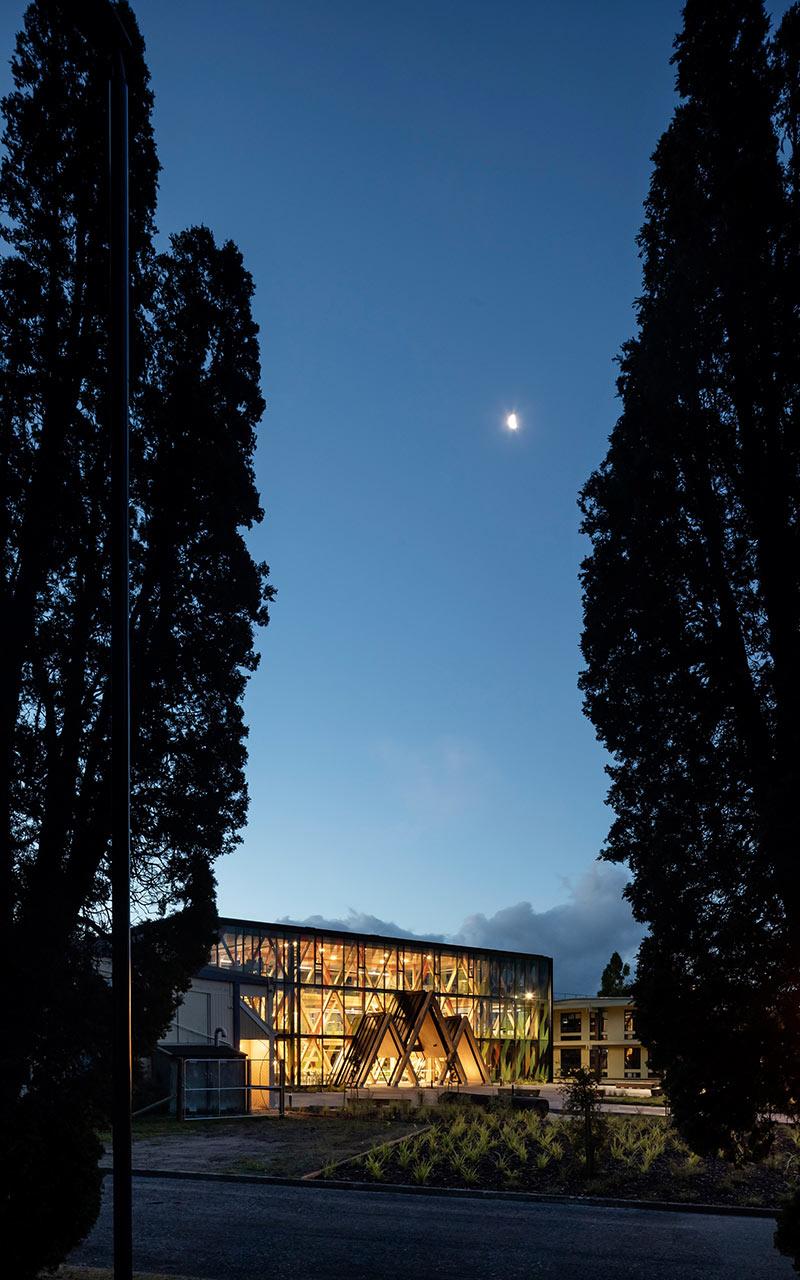
The building’s energy-efficient operation is ensured, among other things, by the rear-ventilated double façade and the patterned glass coating, which reduces the amount of sunlight entering the building. This pattern, as well as the carved ornamentation on the entrance portal, was also inspired by the local Maori people.
Indigenous construction methods are circular
Inclusion of New Zealand’s indigenous peoples is more than just lip service. Apart from the formal design elements, the state institute, which researches timber construction, has a close partnership with these tribes. After all, the traditional Maori meeting houses, known as Wharenui, are still made from carved wooden components today.
The traditional knowledge that many indigenous peoples have about circular building with materials from nature can thus be incorporated into current research. And thus point the way to a climate-neutral future.
Text: Gertraud Gerst
Fotos: Patrick Reynolds
iThere are no comments
Add yours